
Therefore, when positioning control, it is positioned by subdivided 2-phase or 1-phase conduction.
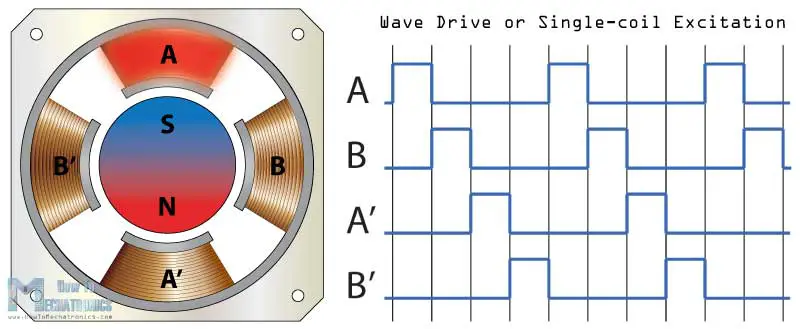
The following figure is a schematic diagram of the motor stator current sequence in a half-step drive mode: Compared with the whole step method, the half-step method has the advantages of double the precision and less vibration at low-speed operation. In this cycle, the two-phase coil is single-phase and then double-phase excited, and the stepping motor will rotate at half a step angle of each pulse.
#Waveform of stepper motor drive driver#
After the driver receives the next pulse and gives two excitations at the same time, the rotor will move half a step angle and stop in the middle of the two adjacent full-step positions. In the case of single-phase excitation, the rotor stops at one position.
#Waveform of stepper motor drive software#
However, the advantage of the full-step drive is that the hardware or software is relatively simple in design so that the drive manufacturing cost is easily controlled. With this driving method, the motor will shake at low speed and the noise will be large.
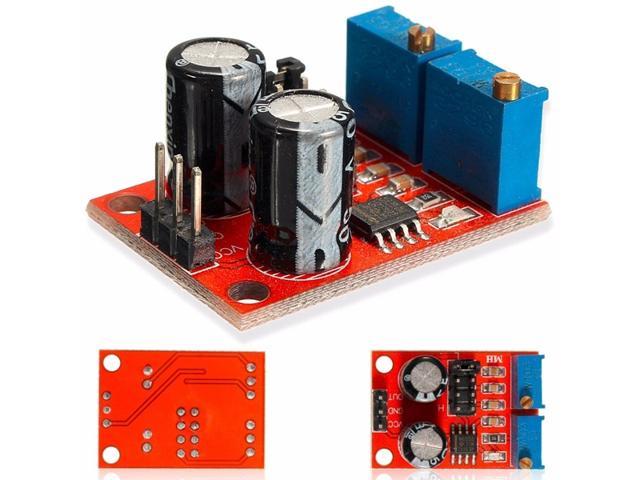
The current vector driven by the full-step divides a circle into four equal parts, and the current waveform is rough.
